Your cart is currently empty!
How Ash Is Helping ASU Achieve Its Sustainability Promise
Back in 2018, Arizona State University (ASU) proposed to construct a US$192 million Interdisciplinary Science and Technology Building that would be both striking and reflective of campus history; whilst being as sustainable as possible during its construction and lifetime. Construction began in January 2019 and has recently opened for usage by students.
Sustainability As A Priority
ASU has a detailed and rigorous sustainability promise that involves achieving carbon neutrality by 2035 and supporting the circular economy by adapting and using circular resources wherever possible.
As a result of this promise, the project research team decided on a fly ash concrete mix for the new building. Tom Reilly, a principal and architect with Architekton explains the final decision, “A lab building really needs to be a concrete frame, and concrete has a pretty big (carbon) footprint, So the team immediately started to look at ways we could reduce that footprint and came up with a couple of unique ones,” he said.
The overall goal was to reduce the total amount of concrete by at least 40%. Contractor McCarthy Building Companies worked with Hanson Aggregates, structural engineer Buro Happold, and fly ash supplier Salt River Materials Group to develop concrete mixes that successfully employed a 40 per cent substitution of Class F fly ash for portland cement, finishing the project having used roughly 20,000 cubic yards of concrete.
The high fly ash mix was used for structural concrete required to achieve a range of strength requirements for elements including slabs, decks, walls, and columns. Beyond the concrete mix’s strength and sustainability requirements, the mix can also be seen within the building. The mix appears in the building’s stairs, eaves and floors, achieving the required aesthetic finish requested by designers.
To reduce the amount of concrete needed further, Buro Happold engineers embedded hollow plastic balls in the concrete.
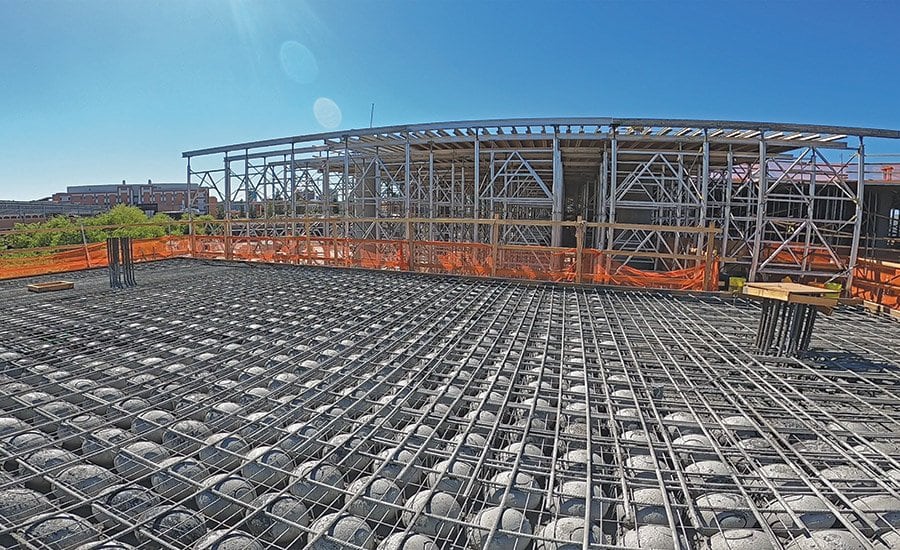
– The BubbleDeck system. Credit: McCarthy Building Companies, Hanson Aggregates, ASU, Architekton.
The ‘BubbleDeck’ system reduces both the amount of concrete needed and the weight of each slab by maximising space and saving money. The lower weight of these structural slabs, in turn, allowed for reductions in the weight and size of other weight-bearing elements.“That’s less mining, less processing, less trucks on the road. That’s less hours the project has to operate to place and pour concrete. So it really does have a big effect to incorporate this rare system that hasn’t been widely used within the United States,” said Carlos Diaz, project director at McCarthy.
Another success story for ash!