Your cart is currently empty!
Report Update: High-density Geopolymer Concrete at Port Kembla’s Northern Breakwater
The University of New South Wales has published its 2nd monitoring report on the in field performance of High-density Geopolymer Concrete (GPC) used in the fabrication of Hanbar amour units and placed at Port Kembla’s Northern breakwater during 2018/9. Download copy of full report here.
This Australian Government led initiative is funded by the Cooperative Research Centre (CRC) for Low Carbon Living Ltd, with financial contributions through the Ash Development Association of Australia (ADAA) and Australiasian (iron & slag) Slag Association (ASA), and in-kind suport from Wagners and Cleary Brothers.
The anticipated rise in coastal wave energy and the continuing environmental attack from climate change scenarios are predicted to cause casatrophic impact on coastal protection structures, signalling an inherent need for upgrades to withstand the stronger wave actions and higher rates of damage.
To facilitate this need, UNSW research team developed a unique high-density low barbon geopolymer concrete (GPC) incorporating steel furnace slag (SFS) as aggregates, which is about 20-25 per cent heavier than natural basalt occurring as a by-product of steelmaking. This density has significant costal engineering advantages.
This low carbon construction solution means a reduced dependency on fossil fuels and emission intensive constructions materials like POrtland Cement thus, contributing to the target carbon neutrality by 2050.
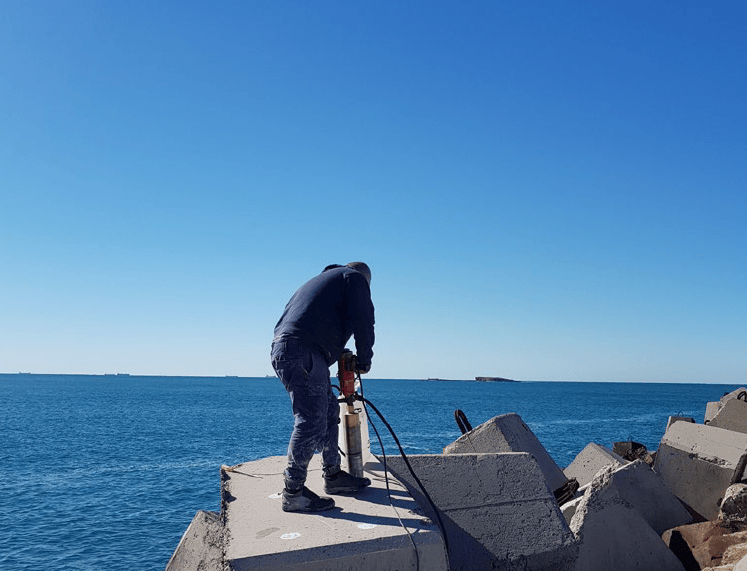
UNSW Researcher collecting core specimens on-site for testing and evaluation
Extensive trials were undertaken by the UNSW research team, to determine the benefical use of steel furnace slag (SFS), both fine and course as concrete aggregates in a predominantly low calcium binder using GGBFS and fly ash. After formulating several mix designs comprising of exclsuively slag cement and fly ash for the binder, researchers observered that SFS aggregates did not display and adverse expansion charateristics when used in conventional concretes. Furthermore the mix designs performed well in ambient curing environment for strength gain.
The laboratory mix utilised 65% fly ash and 35% ground granulated blast furnace slag by mass, respectively, activated with an alkaline solution of sodium hydroxide and Grade D sodium silicate solution blended in proportions to maintain a modulus ratio of 1.5 and a Na2O percentage of 5.5. The critical outcome from the trials is the successful incorporation of the SFS aggregates in the mix and thus, achieving a higher density margin.
Following the trials, the laboratory mix design was optimised by Wagners from Toowoomba QLD to adapt to the commercial batching methods (readymix trucks), with concrete batching completed in three pours. A total of thirteen armour units were cast in three pours utilising approximately 90 m3 high-density GPC.
The compressive strength and splitting tensile strength of GPC batched in the lab trials and poured on-site in Port Kembla were evaluated using cylinder specimens cured in air and saline water.
Critical outcomes included:
Lab trialled high-density GPC: steady increase over time with about a 14% rise in compressive strength from four (4) weeks to three (3) years.
Air-cured samples:samples collected (cylinders) from pour 1 and pour 2 show significant strength reduction held in the laboratory water tanks. For instance, with respect to the 90 days strength, pour 1 had 54.6% strength reduction and pour 2 had 33.8% strength reduction in three years from air curing. These results were ‘Test method’ related and future changes are proposed for handling samples.
On-site samples:higher strength than air-cured specimens collected from site pours and conditioned in the laboratory.

High-density GPC harbar units loacted on shore
The utilisation of steel furnace slag (SFS) in low carbon Geopolymer Concrete (GPC) offers a unique concrete product to upgrade the coastal breakwaters to withstand climate change scenarios, save material consumption, and allow for greater stability without restructuring current Hanbar amour unit designs.